RESEARCH
微小径切削工具による高精度・高能率加工
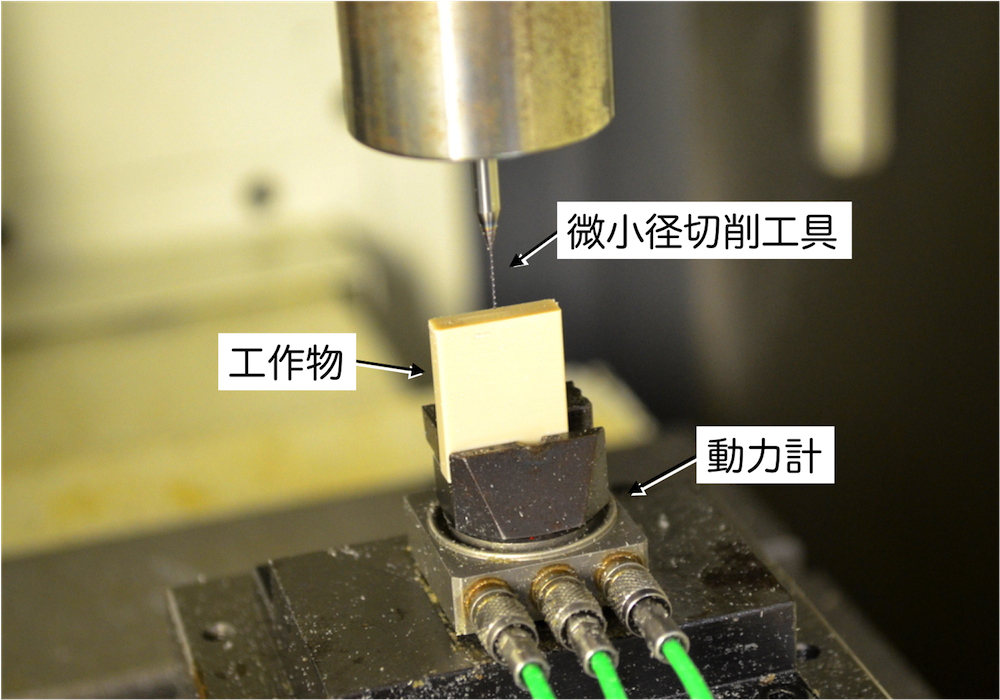
髪の毛よりも細くて人の目で確認することが難しい切削工具(エンドミル、ドリル)を用いて、
難削材と呼ばれる金属材料などの高精度・高能率加工の実現を目指しています。
切削加工は、他の加工方法(放電加工、レーザ加工など)と比較して加工工程が少なく加工時間を短縮、
高精度、設備が安価、金属材料やセラミックスなど様々な材料を加工可能など、多くの利点が挙げられます。
しかし、微小径切削工具は工具径が非常に小さいため、工具が低剛性で加工時に発生する切削力により弾性変形しやすく、
かつ折損しやすい欠点があります。私たちは、加工中の切削力や温度などを測定し、微細切削の切削メカニズムを明らかにし、
高精度・高能率加工へと発展させていきます。
超音波や磁場を援用した研削・研磨技術の開発
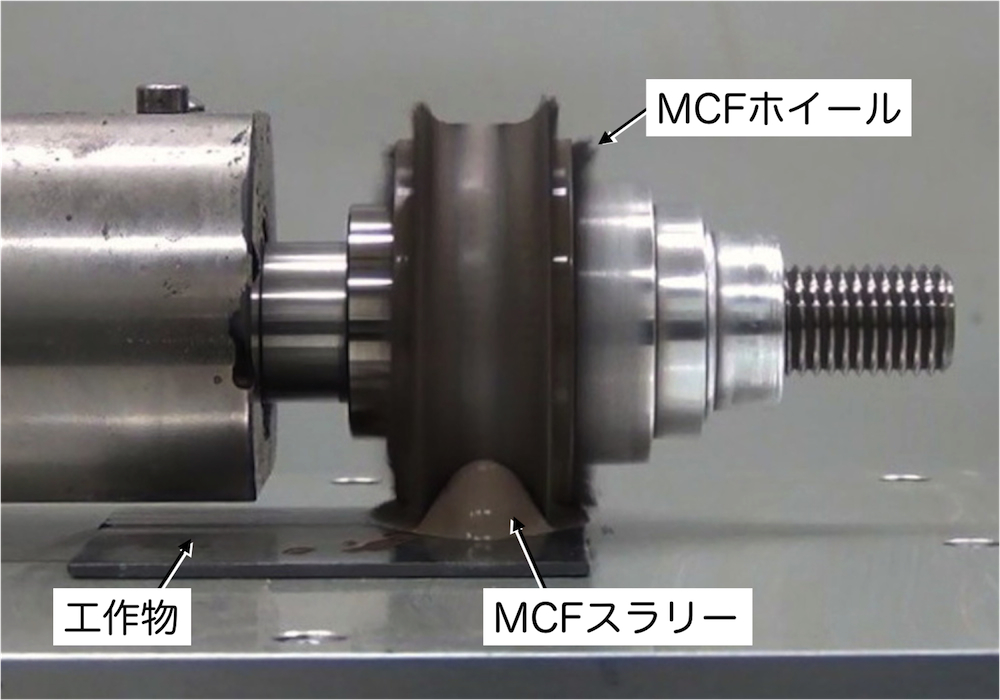
プラスチック製µ-TASチップや太陽光発電用集光フレネルレンズなどを高精度・高能率・低コストで製造するため、 金型の長寿命化や微細形状の高精度仕上げが求められています。これらの要求に対して、 現在では金型の材料としてタングステンカーバイドやSiCセラミックスなどが期待されています。 これらの材料は高硬度かつ高温特性や耐食性に優れている反面、精密加工が非常に困難な難削材とされています。 私たちは、従来の精密加工技術に超音波や磁場を援用した「超音波援用研削技術」や「磁気混合流体(MCF)を用いた精密研磨技術」を開発し、 高硬度金型材料の精密加工を実現します。
微小材料評価技術の開発
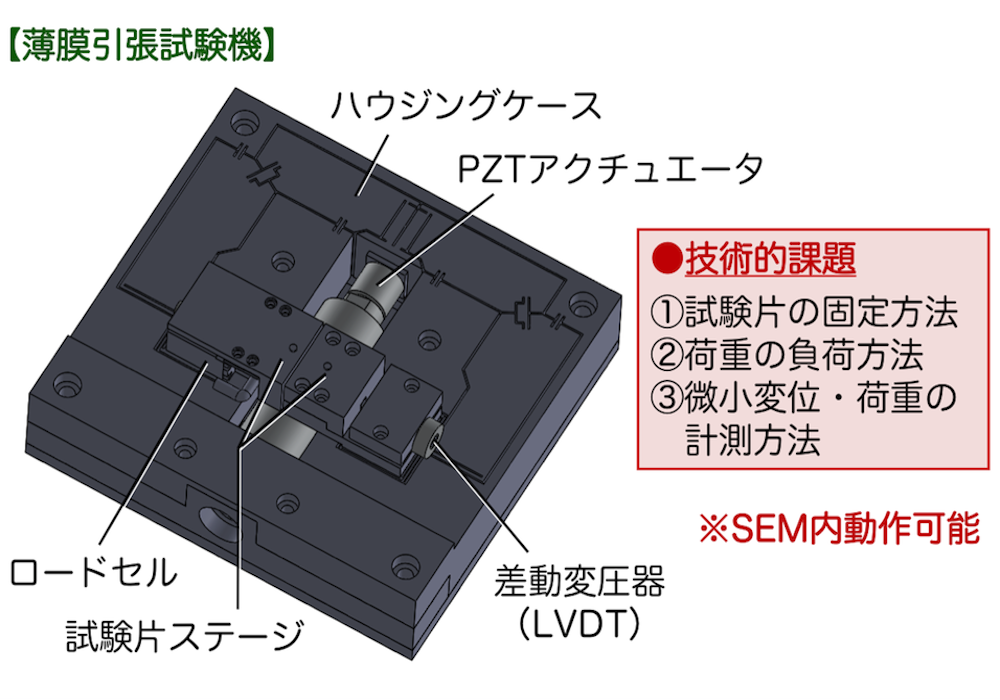
マイクロ・ナノマシン(MEMS/NEMS)は、多種多様な薄膜材料が使用されており、それらの積層構造で構成されています。
これら微小機械デバイスの高信頼性化には、構成材料の使用寸法下における機械的特性を十分に評価し、デバイス設計に反映することが重要となります。
バルク材料の機械的特性(ヤング率、降伏応力、破壊強度など)は、引張試験などで得られた応力-歪み関係から導出することが可能であり、
これまでに数多くの実験がなされて有益なデータが得られています。しかし、評価対象が薄膜材料(マイクロ〜ナノスケール)の場合、
機械的特性の直接計測は技術的に極めて困難となります。
私たちは、MEMS/NEMS用薄膜材料の機械物性を定量評価することを目的として、
薄膜試験片に対して引張負荷や曲げ負荷を付与可能な小型材料試験機の開発を行っています。